Metallbohren mit anschließender Prüfbildanalyse
Zusammenfassung
In dieser Fallstudie wird ein Metallbohrvorgang mithilfe einer nachgelagerten Prüfkamera überwacht. Die rechteckigen Metallplättchen werden nach festgelegter Geometrie mit Löchern verschiedener Größen angebohrt und dann auf ein Förderband fallengelassen. oddy kann dabei aus den Prüfbildern die Plättchen vermessen, die Bohrlöcher verifizieren, sowie die fotografierte Seite auf Kratzer untersuchen.
Durch den Einsatz von oddy lassen sich die fehlerbezogenen Stückkosten von 0,04800€ um 81,8% auf 0,00875€ reduzieren. Durch detaillierte Darstellungen und Kennzahlen lassen sich zudem beschleunigt Rückschlüsse bei einer Anlagenfehlfunktion ziehen.
Prozessaufbau
Ein rechteckiges Metallplättchen wird mit von einem Metallbohrer mit Löchern verschiedener Größen versehen. Danach fallen die Metallplättchen auf ein Förderband, wobei sie auf rechts oder auf links landen können.
Über diesem Förderband ist eine Prüfkamera montiert, welche jedes Plättchen fotografiert. Mithilfe dieser Bilder wird für jedes Plättchen geprüft, ob die Bohrlöcher richtig positioniert sind und die Oberfläche keine Kratzer hat.
Die folgende Abbildung zeigt eine Aufnahme der Prüfkamera vor dem Hintergrund der Transportrollen des Förderbandes.
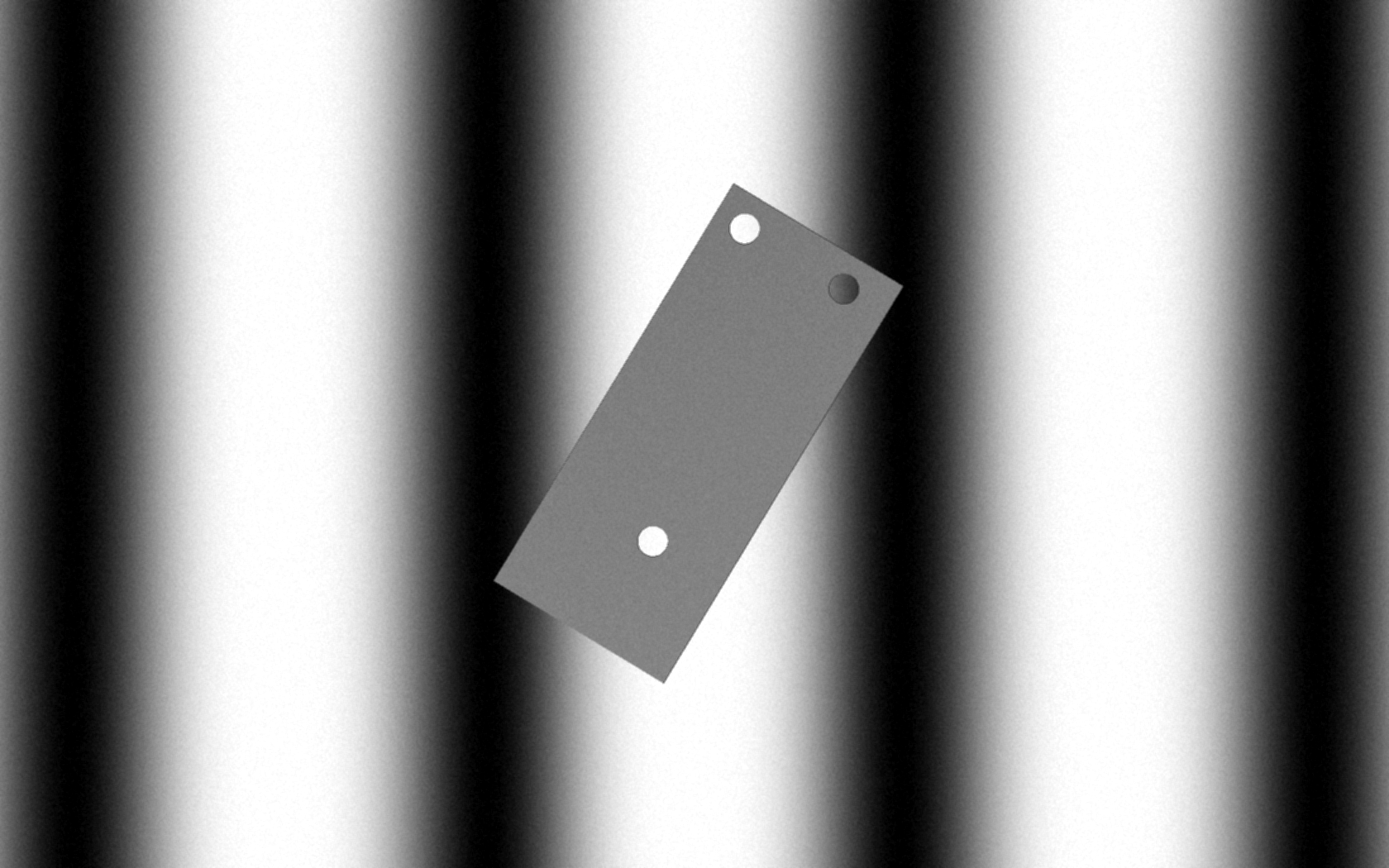
Konfiguration
Die Auswertung und Überprüfung des Bohrprozesses erfordert, dass die Prozessparameter möglichst genau bekannt sind. Um das Prozessergebnis zuverlässig zu vermessen, müssen die geometrischen Parameter der Bohrlöcher und des Plättchens bekannt sein. Zudem muss die Justierung der Kamera über dem Förderband in die Analyse einfließen, um das Bild korrekt zu vermessen.
Aus den Parametern des Plättchens und der Anordnung der Löcher kann dann eine Objektschablone ermittelt werden, die in den Prüfbildern gesucht, markiert und vermessen wird.
Objektgeometrie
Die Objektgeometrie beschreibt die Soll-Dimensionen des Metallplättchens und seiner Bohrlöcher.
-
Plättchenlängen [mm|mm]
Die Breite und Höhe des rechteckigen Plättchens.
-
Bohrlöcher
Die Position [mm|mm] und der Radius [mm] der Bohrlöcher. Die Position wird relativ zum Mittelpunkt des Rechtecks angegeben.
Die Darstellung zeigt die Objektschablone einer Fertigungsform mit drei Löchern.
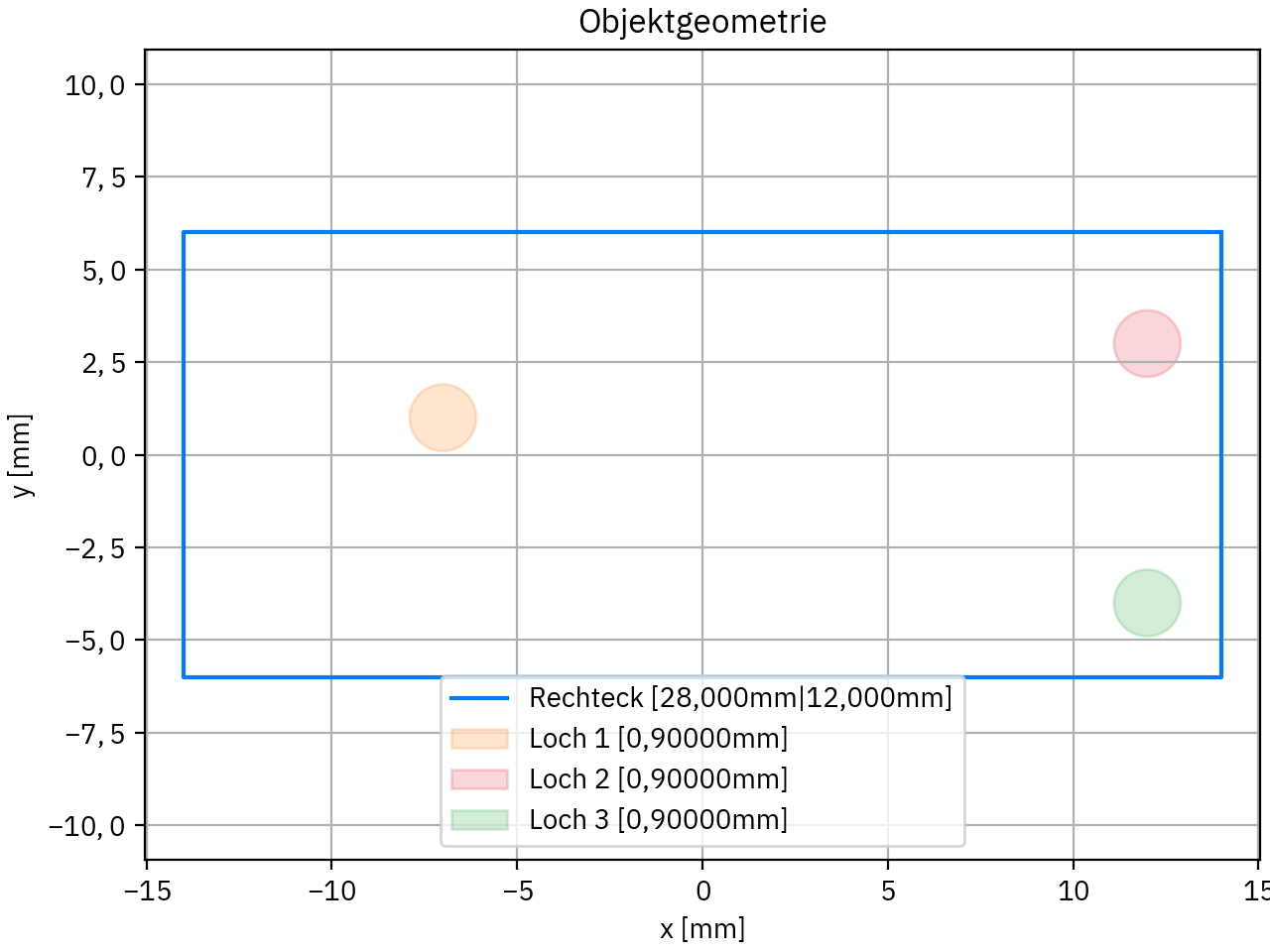
Kamerakalibrierung
Die Kalibrierung der Prüfkamera enthält folgende Informationen:
-
Bildauflösung [px|px]
Die Bildauflösung ist die Auflösung der Grauwertbilder, die die Prüfkamera liefert.
-
Skalierung [px/mm]
Die Skalierung gibt an, wie sich die Pixel auf dem Bild in physikalische Längen in der fokussierten Ebene der Kamera übersetzen.
Die folgende Darstellung zeigt den Fokus der Prüfkamera auf das Schema eines Metallplättchens mit den erwarteten Bohrlöchern.
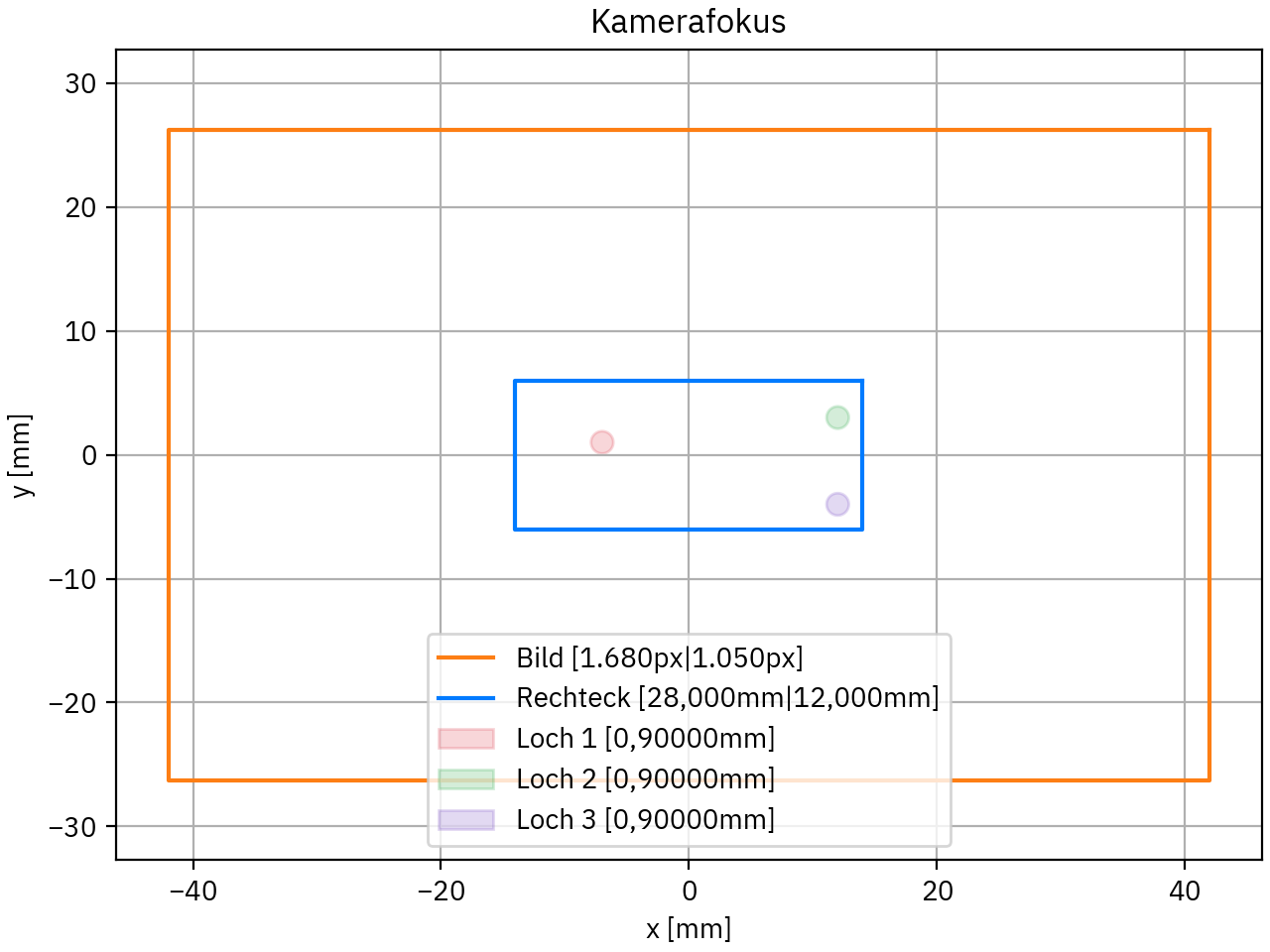
Messung
Die Prüfkamera lichtet jedes Plättchen genau einmal senkrecht von oben ab. Da das Plättchen aus der Bohrhalterung auf das Förderband fällt, landet es verstreut innerhalb eines Zielbereichs auf einer seiner zwei Seiten (auf links / auf rechts).
Die Helligkeit des Bildes variiert über den Tagesverlauf. Zudem sorgen Lichtreflektionen ab und zu für einen Helligkeitsverlauf auf der matt schillernden Oberfläche. Im Hintergrund sind die Schattenreflektionen der Rollen des Förderbandes zu sehen.
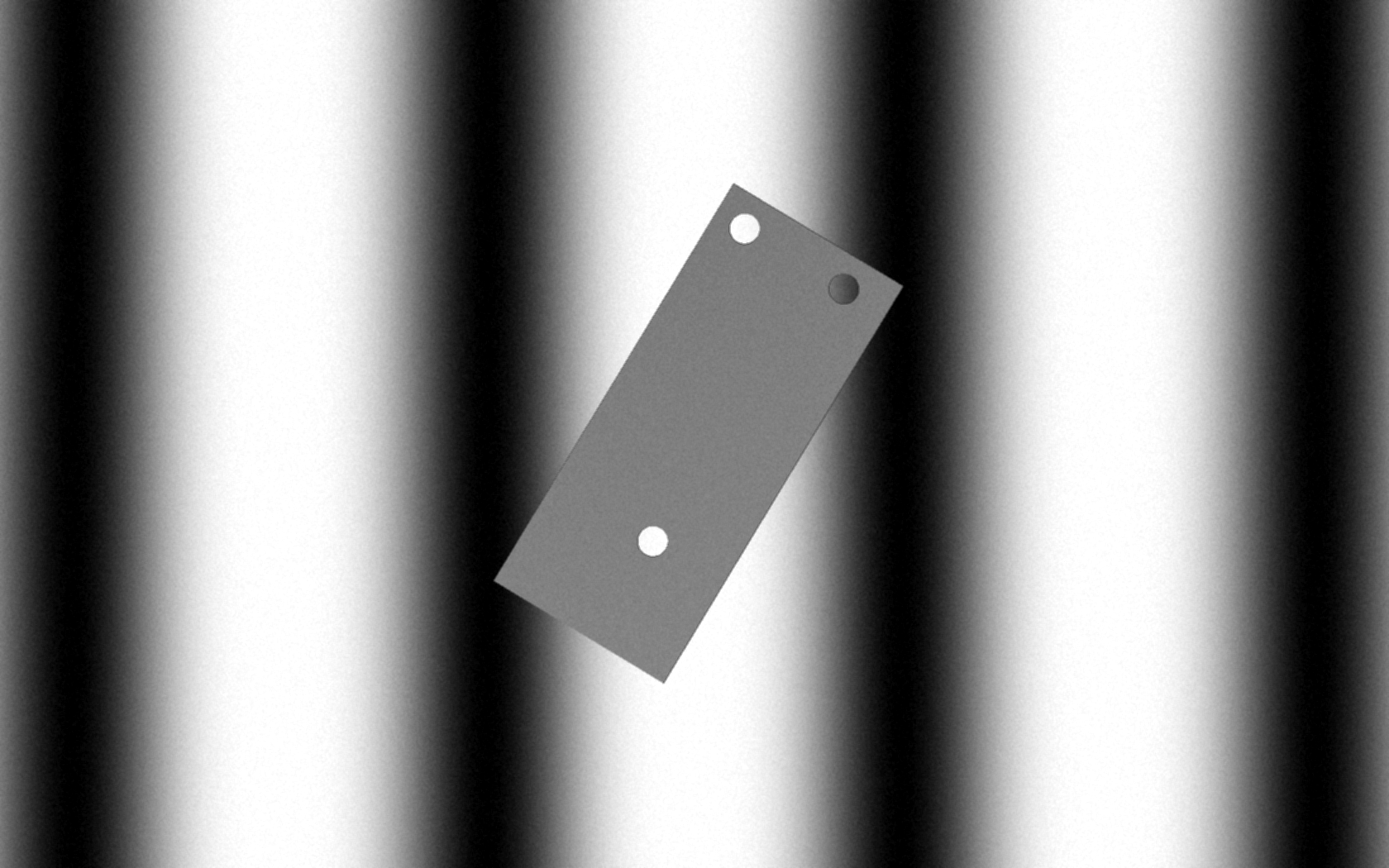
Analyse
Das Metallplättchen soll auf die korrekte Lage und Größe der Bohrlöcher überprüft werden. Zudem soll die sichtbare Seite auf Kratzer in der matt schillernden Oberfläche untersucht werden.
Technische Bewertung
Kantenvermessung
Zur Vermessung des Plättchens muss zunächst das Plättchen auf dem Bild lokalisiert werden. Das geschieht am effizientesten mittels einer Kantenvermessung. Bei der Kantenvermessung wird das Bild so transformiert, dass nicht mehr der Grauwert des Bildes, sondern dessen lokale Schwankung angezeigt wird. Dadurch werden Kanten hervorgehoben und gleichmäßig eingefärbte Bereiche ignoriert.
Die folgende Abbildung zeigt das Kantenbild des vorigen Prüfbildes.
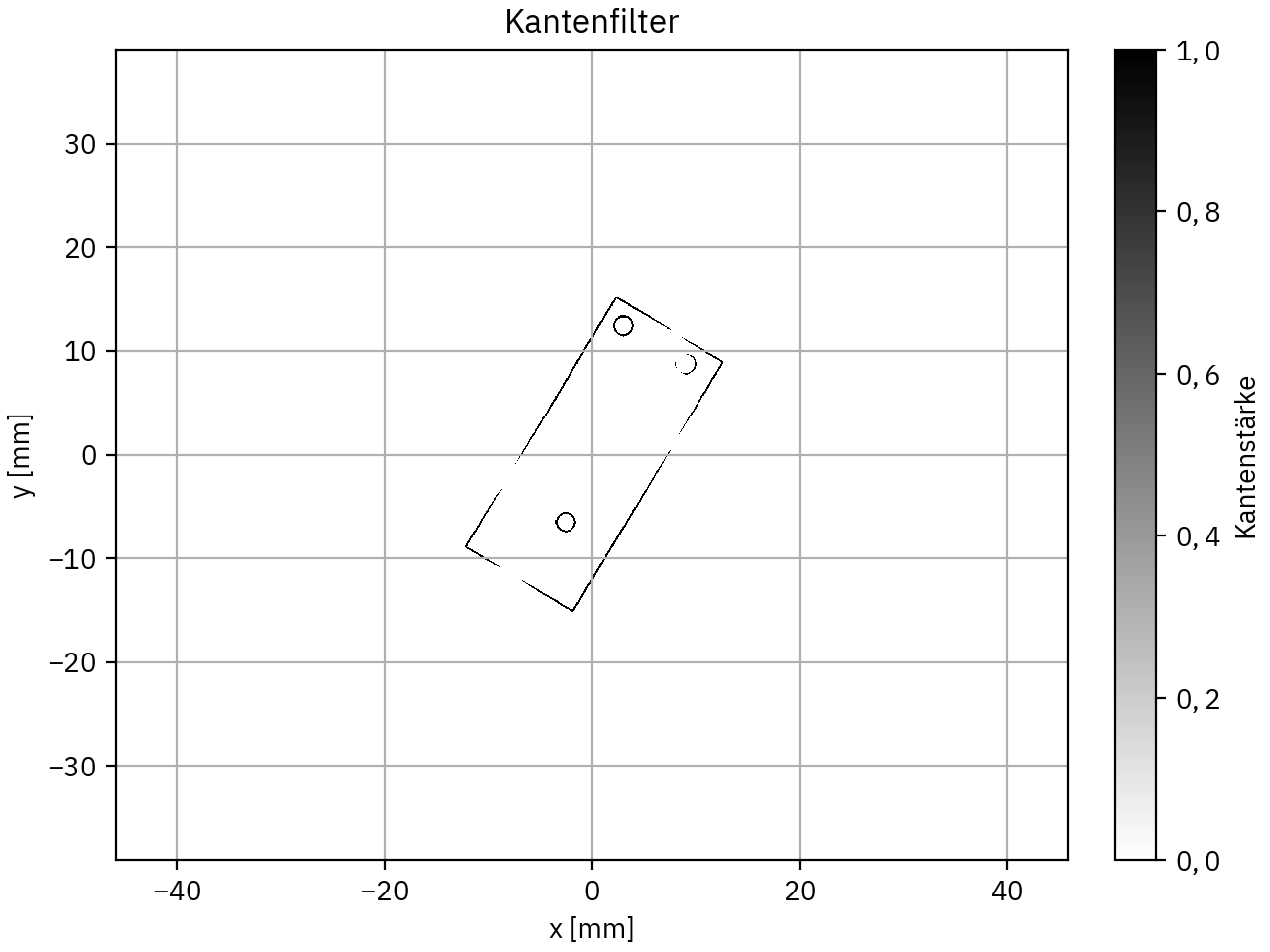
Von der zu identifizierenden Objektschablone wird nun ebenso ein Kantenbild erzeugt. Durch rotieren und verschieben kann diese Kantenschablone dann auf das Kantenbild des Plättchens abgepasst werden. Dadurch werden folgende Lageparameter bestimmt:
-
Position [mm|mm]
Die Position des Zentrums des Plättchens im Prüfbild
-
Rotation [°]
Die Rotation des Plättchens im Bild
-
Spiegelung
Der Parameter, ob das Objekt auf links oder auf rechts liegt.
-
Zoom [x]
Ein Korrekturfaktor nahe bei 1, der den Autofokus der Prüfkamera berücksichtigt.
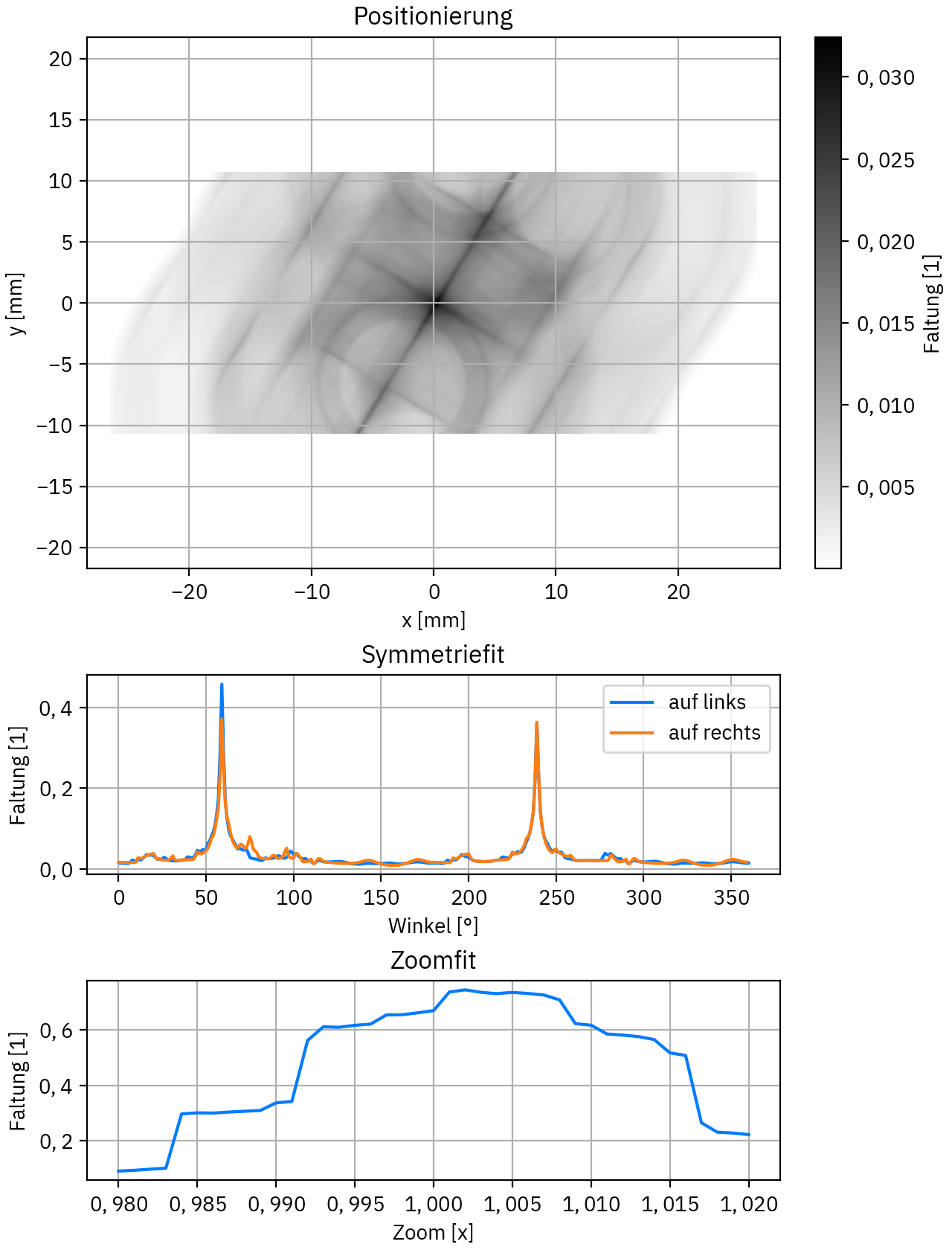
Strukturvermessung
Bei der Strukturvermessung werden die Bohrlöcher auf die richtige Form und Positionierung untersucht. Dazu wird die Umgebung eines Bohrloches gemäß der Objektschablone in Objektpixel und Nicht-Objektpixel eingeteilt. Damit werden dann innerhalb der zwei Bereiche die Farbverläufe gemessen.
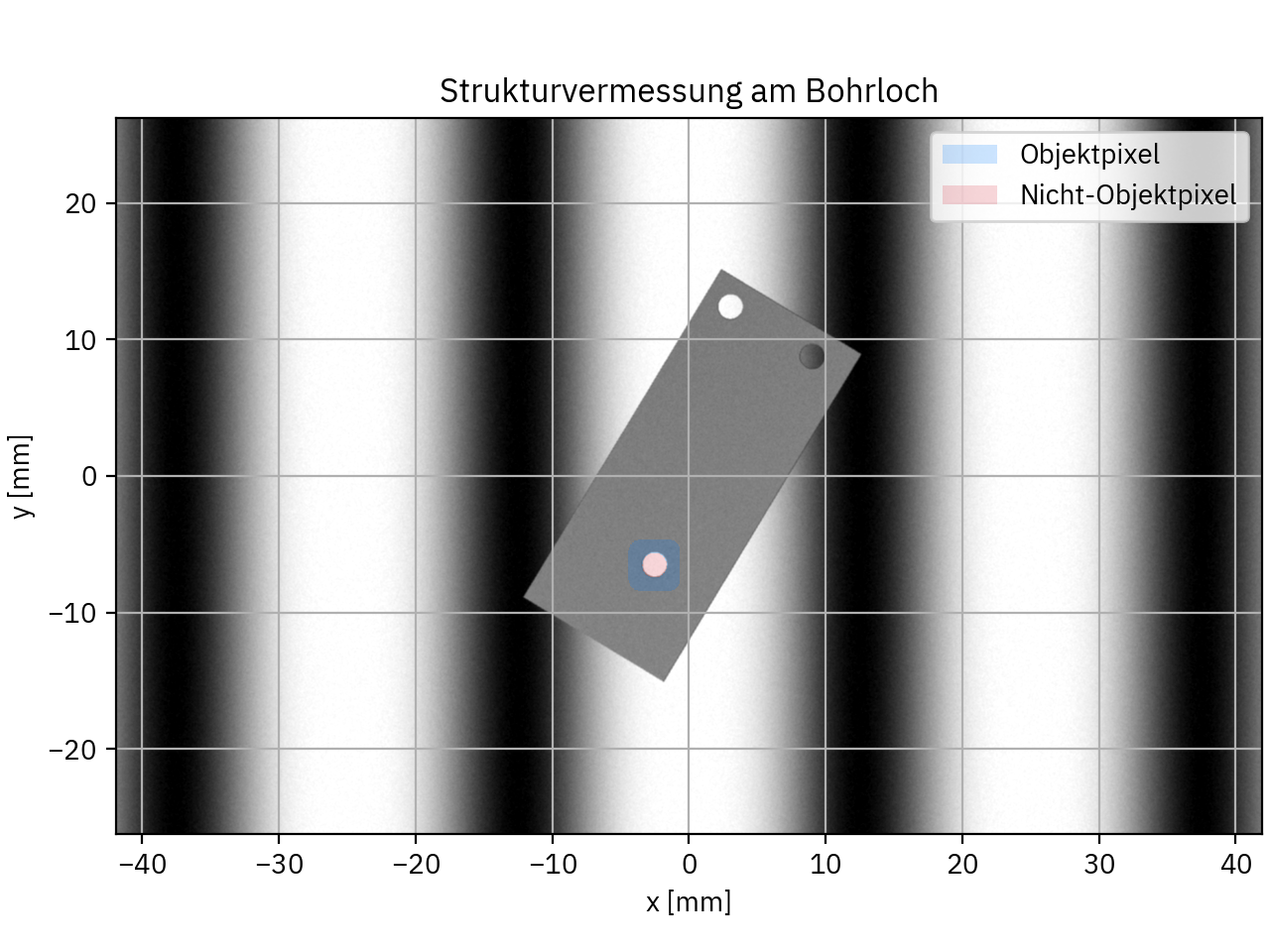
Die Pixel, welche ihrer Farbe nach nahe am mittleren Grauwert der lokalen Objektschablone liegen, werden zum Objekt gezählt. Solche Pixel, die weit vom mittleren Grauwert entfernt liegen, werden zum Hintergrund gezählt.
Damit ergeben sich die Kennzahlen Füllbewertung (Objekt) und Hintergrundbewertung (Nicht-Objekt) wie folgt:
Liegen beide Kennzahlen nahe 1, ist die Struktur gut erkannt worden und korrekt gefertigt. Liegt nur die Hintergrundbewertung niedrig, fehlt möglicherweise das Bohrloch oder ist zu klein. Liegt nur die Füllbewertung niedrig, ist das Bohrloch möglicherweise zu groß.
Kratzervermessung
Zur Kratzervermessung werden innerhalb der glatten Flächen des Plättchens Kanten gesucht. Es werden solche Pixel als Kratzer markiert, deren lokale Grauwertvariation um ein Vielfaches über der über die Fläche gemittelte lokalen Grauwertvariation liegt. Solche Kratzer werden dann nach Länge gefiltert. Zudem werden solche Kratzer ausgenommen, welche unmittelbar an der Objektgrenze liegen.
Die folgende Darstellung zeigt ein Prüfbild mit einem identifizierten Kratzer.
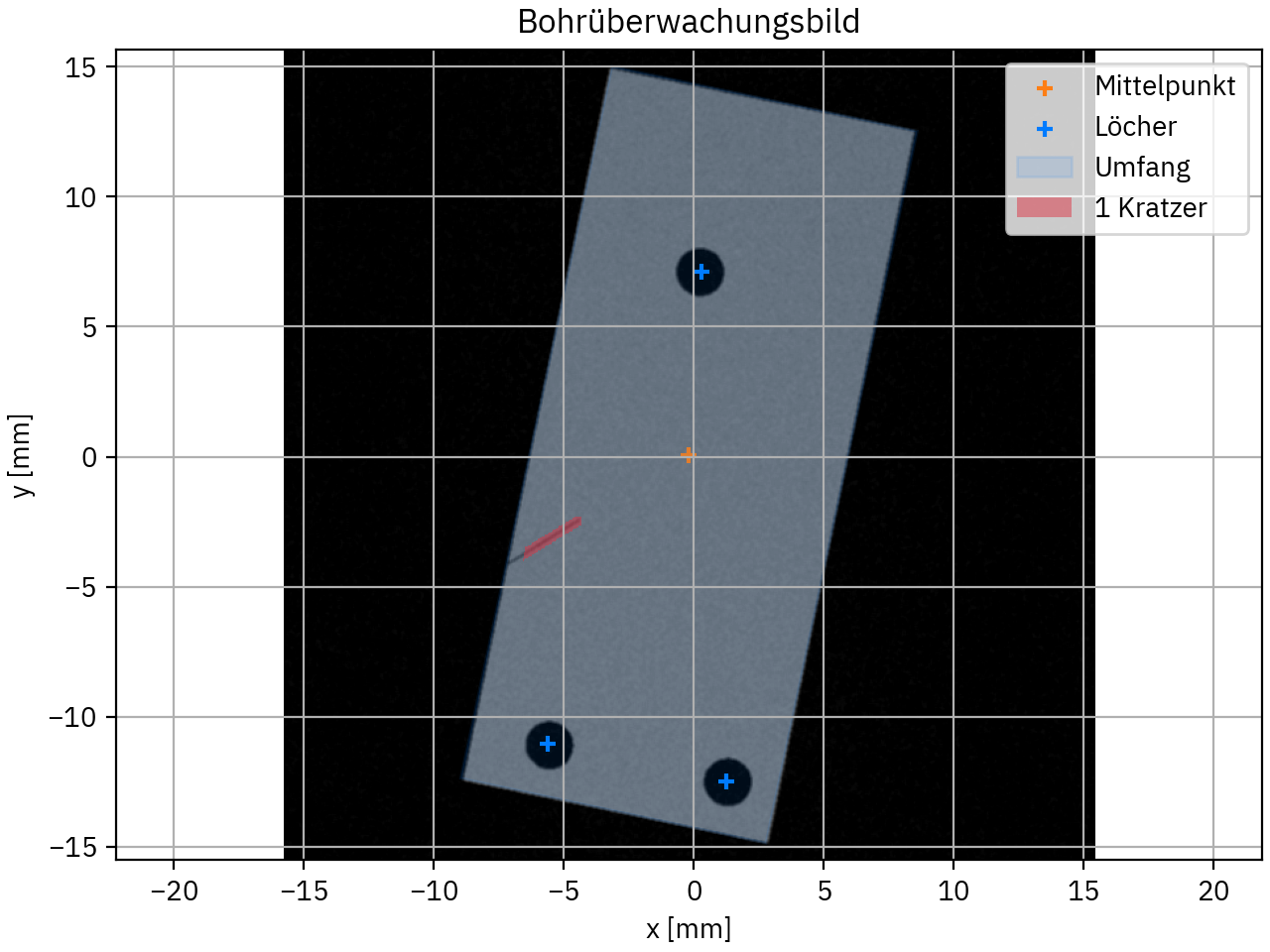
Wirtschaftliche Analyse
Um die Zuverlässigkeit der Methodik und der Schwellwerte, sowie den wirtschaftlichen Nutzen der Qualitätskennzahlen einzuschätzen, kann man die Trennschärfe der Methodik für eine Bauteilstichprobe bestimmen, deren Qualitätsmerkmale auf anderem Wege bekannt sind.
-
Defekt ausgeliefert - falsch OK
Das Bauteil ist nicht OK, aber der Fehler wird nicht bemerkt. Das Bauteil wird trotzdem ausgeliefert und verursacht Folgekosten durch Reparatur, Ersatz oder Reputationsverlust.
-
Fehlerfrei entsorgt - falsch nicht OK
Das Bauteil ist OK, wird aber fälschlicherweise anders eingeschätzt. Das Bauteil wird entsorgt und abgeschrieben, obwohl es hätte verkauft werden können.
Typischerweise sind defekt ausgelieferte Bauteile wesentlich teurer als fehlerfrei entsorgte. Dementsprechend können die Schwellwerte genau nach betriebswirtschaftlichen Einschätzungen eingestellt werden.
Die folgende Abbildung zeigt eine beispielhafte Verteilung für eine Stichprobe von 1.000 Bauteilen.
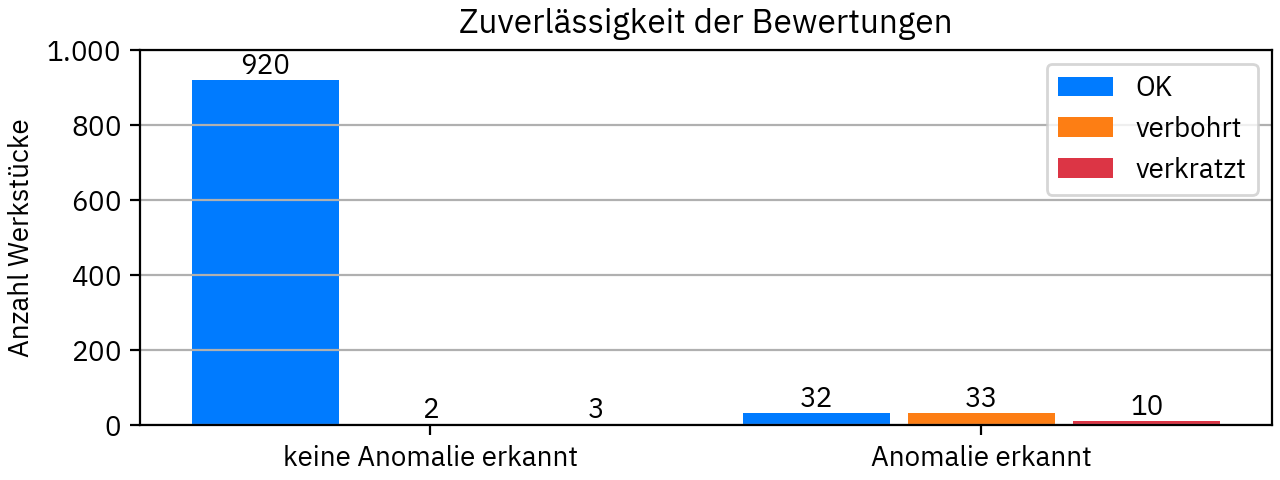
Dafür ergibt sich folgende Bewertungsgüte.
Bauteile | Bewertung | Merkmal | Anzahl | Anteil |
---|---|---|---|---|
gesamt | 1.000 | 100,0% | ||
keine Anomalie erkannt | 925 | 92,5% | ||
OK | 920 | 92,0% | ||
verbohrt | 2 | 0,2% | ||
verkratzt | 3 | 0,3% | ||
Anomalie erkannt | 75 | 7,5% | ||
OK | 32 | 3,2% | ||
verbohrt | 33 | 3,3% | ||
verkratzt | 10 | 1,0% |
Nimmt man nun an, dass ein defekt ausgeliefertes Bauteil Folgekosten von 1€ und ein entsorgtes Bauteil Abschreibungen von 0,05€ verursacht, ergibt sich damit die folgende Fehlerkostenschätzung:
QS-System | Fehlerquelle | Quote | Kosten / Fehler | Kosten / Teil |
---|---|---|---|---|
ohne oddy | 4,8% | 0,04800€ | ||
defekt ausgeliefert | 4,8% | 1,00€ | 0,04800€ | |
defekt entsorgt | 0,0% | 0,05€ | 0,00000€ | |
fehlerfrei entsorgt | 0,0% | 0,05€ | 0,00000€ | |
mit oddy | 8,0% | 0,00875€ | ||
defekt ausgeliefert | 0,5% | 1,00€ | 0,00500€ | |
defekt entsorgt | 4,3% | 0,05€ | 0,00215€ | |
fehlerfrei entsorgt | 3,2% | 0,05€ | 0,00160€ |
In diesem Szenario ergibt der Einsatz von oddy im Vergleich zu einem QS-System, welches die detaillierten Fehlerbilder nicht erkennt, eine erwartete Kostenreduktion um 81,8% durch verbesserte Qualitätskontrolle von 0,048€ auf 0,00875€ pro Bauteil.
Fazit
Durch die prozessbezogene Prüfbildanalyse kann oddy Fehlerbilder identifizieren, die im Bohrvorgang entstehen können. Durch diesen Vorteil ist es möglich, die Fehlerfolgekosten von defekt ausgelieferten Bauteilen drastisch zu reduzieren. Zusätzlich liefern detaillierte Prozesseinblicke die Möglichkeit, den Betrieb mit erhöhten Fehlerraten zu analysieren und zu intervenieren.
Die für diese Fallstudie verwendeten Prozessdaten sind zu Demonstrationszwecken streng zufällig erzeugt worden.